Why we need to decarbonize cement, with Sublime Systems’ Leah Ellis
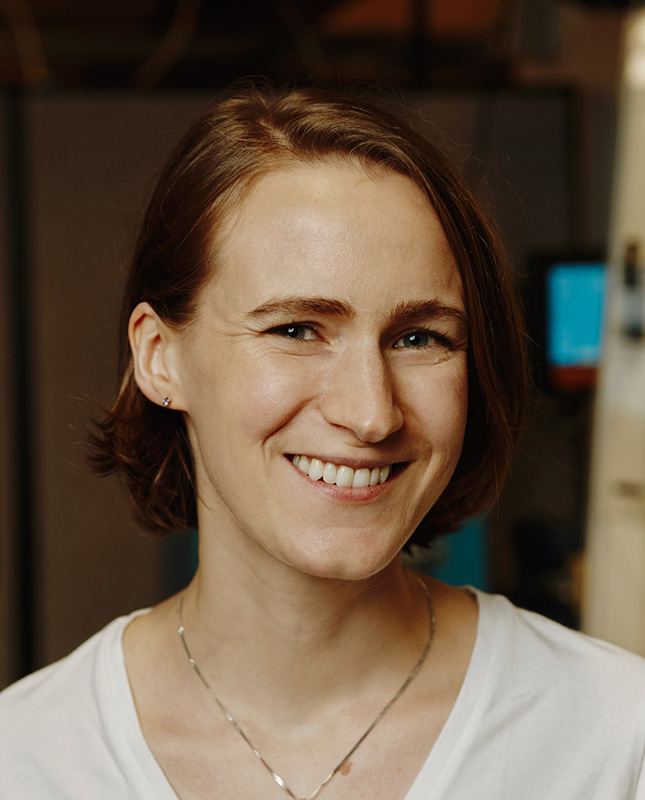
Listen and Follow ‘Good Clean Energy’
On this episode, Jim is joined by Leah Ellis, co-founder and CEO of Sublime Systems, to discuss why we need to decarbonize cement.
Cement accounts for 8 percent of global CO2 emissions and is the biggest industry by mass in the world, Ellis said. The production of one ton of Portland cement — the kind most commonly used — results in one ton of CO2 released into the atmosphere. And since cement is exceptionally cheap and the most massively produced man-made material in the world, those emissions are going to grow. “In a do-nothing scenario, emissions from cement are projected to increase 50 percent between now and 2050,” Ellis said.
But Ellis’ company is producing low-carbon cement by replacing the traditional high-temperature, fossil fuel, combustion-driven kiln with an electrochemical approach that operates at ambient temperature, using renewable electricity, ultimately making that high-performance cement that we’ve been using for millennia, she said.
“I like to say Sublime is the electric vehicle of cement making.”
Covered in this episode:
- [3:18] How Ellis’ background in chemistry led to making carbon-free cement
- [5:51] Why defining cement by its performance is important
- [7:48] The basics of cement
- [9:29] The outrageous amount of cement produced annually
- [11:29] How Sublime Systems produces cement with fewer carbon emissions
- [18:06] The ability to compete economically
- [23:04] Scaling up Sublime’s operations
- [26:37 The leaky tap analogy to understand the climate crisis
- [29:53] A vision for the cement industry in 2035
The following transcript has been edited for clarity.
Just about 200,000 years ago, homo sapiens trucked out of the African Savanna and started becoming, really, the alpha predator on the planet. And it wasn’t until 12,000 years ago that they figured out how to sow seeds and grow crops. And once homo sapiens were able to kind of stay in one place and discover agriculture, they needed a dwelling. They couldn’t just always live in caves and trees, and so they started building things.
And over the years, they started developing new materials. So it wasn’t just dirt and sticks and cow dung and clay. It was cement.
Going back thousands of years, the Romans discovered how to put some elements together that formed a mortar, that they could stick stones together, or they could actually make concrete. Concrete that they could even put in the water and make piers. They can make the Colosseum and the Pantheon.
Well, fast forward to today, the built world — the world built by humans for our benefit, the roads, the bridges, the houses, the sidewalk you walk on to work every day — this material represents the largest amount of mass on the planet. Our built world outweighs all of nature: plants, animals, fish, fungi, algae. This is an amazing, amazing achievement.
And we’re not done. This 1.1 trillion metric tons of matter that we have assembled is growing. In fact, there are some estimates that say it’s going to grow to be 1.4 to 1.5 trillion tons in the next 20 or 30 years, because we’re not done building bridges and roads and houses and factories and all different types of things. And one of the materials we use to do this, the most manufactured product on earth, is cement and concrete.
And this amazing material is so inexpensive, around $130 a ton. It does come at a cost because for every ton of cement we produce, we produce a ton of carbon dioxide. To put this in perspective, you need to understand that we produce 4 billion tons of cement every year, and we mix it with sand and gravel and other aggregates to make 10 or 12 billion tons of concrete. So as we add to the staggering weight of our built world, we’re also adding to the carbon dioxide that’s in our atmosphere. So how do we continue to meet the needs of the world, to build the roads and the bridges and the factories and the buildings and the homes and the schools and the hospitals without producing more carbon dioxide?
Today on Good Clean Energy, we’re joined by Dr. Leah Ellis, co-founder of Sublime Systems, who has figured out a way to make concrete and cement without releasing carbon into the atmosphere. My name is Jim McNiel, and this is Good Clean Energy.
Jim McNiel: Leah Ellis. Welcome to Good Clean Energy.
Leah Ellis: Thank you so much, Jim. I’m delighted to be here.
McNiel: Let’s start with a little background about how you came into this unique space, especially as a PhD in chemistry. And I think your background was really in the battery space.
Ellis: Yeah, that’s right. I have a PhD in chemistry. I went to the university ten minutes away from the house I grew up in, in Halifax, Nova Scotia, and it just so happened they had brilliant electrochemists there. And so I sort of fell into the orbit of these world-famous scientists who were inventing different pieces of the lithium ion battery for the past 20 to 30 years. And so that was the academic tradition that I came from, and that’s where I really got a passion for invention and using chemistry to create things and to create value and to push the edges of the known.
And so once I finished my PhD, I wanted to do more of that, and I was very lucky to get a Canadian government fellowship that allowed me to go anywhere, work with anyone. And I chose to come to MIT to work with Professor Yet-Ming Chiang, who then became my co-founder. And he also is a prolific inventor, also a battery scientist. So he has spun out six other companies out of his lab before Sublime Systems, and most of them are electrochemical, battery startups. Most recently Form Energy, long-duration energy storage. So I simply wanted to work with someone who was inventing things that would assist with climate change. And it was his idea, really, to venture outside of batteries.
You know, batteries have been perfected over decades. And so I was delighted that he invited me to think about how we might use electrochemistry and this influx of renewable energy that’s coming on the grid to decarbonize something else. And so the tagline we were working backwards from was “electrochemical cement.” So how might we use renewable electricity and use that to make clean cement? Cement being 8 percent of global CO2 emissions and one of the biggest levers for decarbonization after the energy sector.
The basics of cement
McNiel: So it’s quite a leap for you to go from some of the most advanced science in the world — which is perfecting lithium ion batteries and other battery chemistries — to something that is older than any construction material on earth, which is concrete,. And so, you’re saying that since concrete production annually contributes to 8 percent of carbon emissions, that we need to be able to decarbonize that process. And I think I heard you say once before that, is it a ton of cement is a ton of carbon? Is that the equivalent?
Ellis: That’s right. Although I would like to finesse that a bit. So a ton of Portland cement — which is today’s modern cement that’s made in kilns — one ton of Portland cement results in a ton of CO2, but I want to be careful with saying one ton of cement equals a ton of CO2, because cement doesn’t necessarily have to be Portland cement. There’s a wide class of cementitious materials. Portland cement was only invented around 1850 or so. So we’ve been using this material made in this way relatively recently, but we’ve been using cement for millennia, as you know. And, as we start to decarbonize, cement is no longer synonymous with Portland cement. And the industry is moving towards blended cements and blending Portland cement with limestone and with fly ash and slag and calcined clays and other types of cementitious materials. And what’s important about that trend is that cement is no longer being defined by its chemistry. So for the past 100 years, ASTM International and structural engineers, when they are looking to define cement to be used in their construction projects, they use this code word called ASTM C1157, which really specifies Portland cement by its crystal structure.
McNiel: It’s crystalline structure.
Ellis: Exactly. And now that’s changing as we’re decarbonizing. And because there’s so many different types of cementitious materials that can all chip away at that carbon footprint, that’s where cement is now being defined by its performance and not by its crystal structure.
“One ton of Portland cement results in a ton of CO2.”
Ellis: That’s right.
McNiel: Or other materials. I mean, you can obviously mix cement with all different types of things. And the main thing that is guilty of producing lots of carbon is the production of cement.
Ellis: Yes, that’s right. It is the cement. So, cement is made in these enormous fossil-fueled kilns. So it is the biggest industry by mass in the world. So we use about 4 billion tons of cement per year, 3 billion tons of that being Portland cement. And so Portland cement is made by taking limestone, so calcium carbonate, which is 50 percent by weight CO2, and putting that in one of these massive fossil-fueled kilns that goes first to 900 degrees Celsius to decompose that limestone and to release the CO2 from the limestone to form reactive lime. And then the second step is to heat it to 1,400 degrees Celsius, which is an insanely hot temperature. At which point you can only get to that temperature, effectively and efficiently, by using combustion. So burning, most often coal and bituminous coal, in today’s kilns to get to that temperature at which Portland cement phases form.
The staggering amount of cement produced annually
McNiel: Now Portland cement. So everyone understands when you see a cement truck rolling down the road or someone pulls up at your house and they have a mixer, they’re pouring Portland cement into that machine.
Ellis: It’s either Portland cement or a blend of Portland cement and these other supplementary cementitious materials, and sand and rocks aggregate to make that concrete.
McNiel: And when you say there’s 4 billion tons of cement produced annually, there’s a ratio of about two-and-a-half to three that turns that into concrete. So there’s about 12 billion tons of concrete produced annually.
Ellis: Yeah, so cement is about 10-15 percent of concrete. So really, it’s quite a staggering volume. I’ve heard recently one other stat to sort of put this in perspective. The built environment now has a larger mass than all living things on Earth. And I think much of the built environment and many manmade materials really is concrete. So, that’s just another way to think about the volume of this industry.
“In a do-nothing scenario, emissions from cement are projected to increase 50% between now and 2050.”
Ellis: It’s outrageous. And the outrageous thing is that our consumption of cement is only going to grow, and with it, cement CO2 emissions, if we do nothing. So you know, the world’s population is growing. It’s becoming more urban. And also we need cement more than ever, because cement is such a magical, high-performance material. We really need it to build structures that are going to be resistant to climate change, that are going to endure in extreme weather events. So in a do-nothing scenario, emissions from cement are projected to increase 50 percent between now and 2050. But of course, that’s untenable, because between now and 2050, we have to get to net zero. And so this is where the need for a new type of cement manufacturing comes in. And ideally, a method of making cement that avoids CO2 emissions and avoids fossil fuel, rather than simply, using post-combustion carbon capture, or carbon offsets in order to get to a net-zero or net-negative cement.
How Sublime Systems produces cement with fewer carbon emissions
McNiel: Yeah, better not to do it if you don’t need it, right? I mean, that’s the trick. So, just to put it in perspective, you said it was 8 percent of carbon emissions. I mean, we know that our annual energy budget for carbon production is about 37 gigatons. We now know that we’re producing 4 billion tons of cement. That’s 4 gigatons of carbon, if you use that direct one-to-one correlation. So, yeah, it’s a big deal. And also you were talking about lime. I’m assuming the name “Sublime Systems,” which is your company, is a play on the fact that you’re doing lime differently. Is that what we’re talking about?
Ellis: Yes, that’s right.
McNiel: So tell us how you’re doing it differently. How are you making cement without this incredible heat?
“Sublime is the electric vehicle of cement making.”
McNiel: This is what releases CO2.
Ellis: Exactly. So about 50 percent of the CO2 is from the minerals themselves, which release CO2 as they break down. And then the other is from the fossil fuels needed to get to these extraordinary temperatures.
McNiel: But the first part is, it’s contained in the rock.
Ellis: That’s right.
McNiel: And it’s being released.
Ellis: Yep, it’s a carbonate mineral.
McNiel: In just the same way that carbon is contained in oil that we take out of the ground and when we burn it, we release that carbon.
Ellis: Yeah, that’s a great analogy.
McNiel: So you have two sources of CO2 in the production of cement. One is CO2 that comes from the materials you’re working with and you’re heating up and you’re releasing that sequestered carbon. And the second is the fuel that’s used to operate it, the kiln.
Ellis: And so Sublime goes about a very similar process in the sense that we take an inert mineral and we break it down, we break those inert bonds resulting in a reactive cement powder, but we go about it in a different way. We have an electrochemical reactor, it’s based on a water-splitting reaction. So very similar to a hydrogen electrolyzer, but this time we’re producing acid and base at the two electrodes instead of producing hydrogen and oxygen. And we use that pH gradient between the electrodes to drive chemical reactions. So we’re mitigating the use of fossil fuels, so we don’t have to use fossil fuel. It’s a purely electrochemical process.
And then we also avoid the CO2 emissions from the minerals because we don’t need limestone. We don’t have to break things down thermally. We’re using acid to extract calcium, and we can do that from a wide variety of calcium-bearing inputs. We can use limestone if we choose. And if we do, what results is pure, clean and compressed CO2. And you can think of that like a Mentos and Coca-Cola reaction, when you’re taking a carbonate and reacting it with an acid in a pressurized environment, it results in automatically captured CO2.
But the strength and the beauty of our process is that we are almost agnostic to input materials, so we can extract calcium from a wide variety of sources. And the sources that we’re focused on are our calcium silicate materials, which are very common industrial wastes and common basaltic rocks that we can extract the calcium from, leaving behind a reactive silicate and then we can dry those materials off into separate streams. So a calcium stream, a silica stream, and blend those two together to make a cement.
And this cement is actually very similar to Roman cement. So when Romans made cement, they made lime through the calcination of limestone, so that very fossil-intensive process. And then they mixed that lime with reactive silicates. And they had on-hand volcanic ash and that combination of lime and silica is what makes a great cement. Now you can’t do that nowadays. It would just be just as fossil-intensive as Portland cement, because you’d still be relying on that calcination of limestone. But, now that we can make carbon-neutral lime, that now allows us to go back to that Roman recipe that produces a very strong and durable cement. But now we can do it without carbon emissions and totally avoid the kiln.
McNiel: Well, that’s really, number one, very interesting. You’re going to be able to do this, as you say, at room temperatures, but you’re going to require, obviously, electricity to run this process. And so, what is the source of your electricity, so you can come out and say that you’re building CO2-free cement?
Ellis: Right. So just like that electric vehicle example, the carbon impact of this technology is dependent on the carbon intensivity of the electrons going into it. So it is a very energy-intensive process. And we will have to site next to hydrodams or have sources of other renewables like behind-the-meter renewables perhaps. What is interesting is that because our system is at ambient temperature, we can actually be much more responsive to the grid. Then let’s say if you were to electrify a kiln, and electrify the thermal process, that is not something that is very rampable or responsive because it takes a great deal of time to heat up and to cool down.
“Because our system is at ambient temperature, we can actually be much more responsive to the grid.”
The ability to compete economically
McNiel: Is the energy that you require to run your process less than what you need for a traditional cement kiln?
Ellis: Yeah, ultimately, yes, it will be less. Today, our energy consumption is similar.
McNiel: OK, and when you say ultimately, I mean, obviously you need to scale up to like producing 100 million tons of cement to be a player in that category?
Ellis: That’s right.
McNiel: OK, so is that where you’re thinking you’re going to get to the levels where you can keep your energy costs down below what traditional manufacturers use?
Ellis: It’s both that, and it’s energy consumption. So of course, the larger you are, you can negotiate harder for the price of energy. But speaking about embodied energy, we’re moving quickly to deploy with the technology we have today. So the electrolyzer technology we have, we’re leveraging mostly commercial off-the-shelf electrolyzer equipment that allows us to get similar embodied energy as Portland cement. Ultimately, we do expect to be weaving in new improvements onto the electrolyzer technology that would slow us down if we were to wait for those improvements to the electrolyzer to be perfected. So we are perfecting these improvements to the electrolyzer stack to allow us to get to lower embodied energy. But because Sublime’s mission is to have a swift and massive impact, we’re moving forward with the technology we have. Invention continues to be a big part of Sublime’s culture, so we are continuing to develop a lot of IP on electrochemical synthesis broadly, not just for cement. And so this will result in electrolyzers that are much more efficient in processing minerals than what you can get from electrolyzers today.
McNiel: Well, at the end of the day, the best clean energy solutions are ones that can compete economically, and today Portland cement, I think the average price is about $130. And if I’m going to Home Depot or I’m calling a contractor and he says, “Hey, I’ve got a bag of Portland cement that says it’s carbon-free, and I got a bag that isn’t. They’re the same price. Which one do you want?” If you can compete dollar-for-dollar with Portland cement: game over, you’re going to crush it, no pun intended.
Ellis: The puns are always intended.
McNiel: And if you don’t, well, there’s still a green premium here, right? There’s still value. If I had to pay $20 or $50 more for a ton of cement and it supported my corporate mission, then it’s worth considering. So which do you think is going to be the answer?
Ellis: Well, I think the answer is all of the above. Ultimately we have a path to competing on cost with Portland cement, but right now we don’t have the advantages of scale, and we don’t have those 200 years of technology improvements behind us in the same way that Portland cement has. So, yes, up front, there will be a green premium so to speak, but you can also flip that on its head and say, well, maybe Portland cement has a dirty discount, because all of that pollution is something that you’re not paying for, but that cost really is being paid for somewhere else.
McNiel: If you’re going to be successful in putting a carbon tax on cement, then you know, you should run for president.
Ellis: Yeah, well, actually, the carbon tax on cement is happening in many places, such as Europe. Canada also has a carbon price on fuel. But for the people who are making purchases, I think you’ve hit on an important point, which is cement is exceptionally cheap. It’s the ultimate commodity material. It’s the most massively produced man-made material in the world. And so when you think about that, that’s a double-edged sword. On the one hand, it makes it very difficult for us to compete on cost as a startup that’s building first-of-a-kind technology. So will there be a green premium in the beginning? Yes, there will be a green premium for the coming three to six years. But you can think of that premium in another lens, and you can think of it really, what we’re producing is actually two products in one. We’re producing a ton of cement and we’re also producing a ton of carbon avoidance. And for some people, that carbon avoidance is worth money because like you said, they have corporate goals for net zero, for Scope 3 reduction and people are willing to pay for that. And so when you think of it that way, that really flips it on its head and that weakness becomes a strength, because cement being so inexpensive and so carbon-intensive, really, even if you double the price of cement, what you’re getting in terms of dollars-per-ton of carbon avoidance is really quite compelling when you compare it to other technologies such as direct-air carbon capture, such as sustainable aviation fuel. And I think a lot of people realize that paying these green premiums for emerging technology-enabled carbon avoidance is really important to get over that hump.
Scaling up Sublime’s operations
McNiel: So let’s celebrate some of your victories here. You earlier talked about ASTM C1157, which is the standard that structural engineers look at in order to determine if this concrete that I’m going to make or the cement I’m going to buy is capable of doing the job I need to do. Is it durable? Is it rigid? Is it going to be dependable? Why don’t you fill us in on what happened there? You started to talk about the fact that they changed the rules a while ago to stop looking at the crystalline structure of cement but actually look at the performance of cement.
Ellis: Yeah, that’s right. So as the industry moved to decarbonize and to blend Portland cement with other materials, in 1992 they came up with this performance-based standard. And so, speaking about our accomplishments, we spun out of MIT in March 2020, right at the beginning of the pandemic, and our focus was entirely on scale. So at the time we were making almond-sized amounts of cement at beaker-scale in a lab on the benchtop. And so in three years, we moved very quickly to building our first pilot plant, which we finished right after Christmas. Since then, we’ve had 1,000 hours of continuous operation. We’ve made tons of this material, and we’ve gotten that material not just from the lab-scale, but from the pilot-scale, and we’ve gotten that tested independently by third-party labs to show that it meets all of the performance-based tests that you need in order to define this material as a performance cement.
McNiel: Right now what’s your volume? Are you at the 100 ton level or 1,000 tons? Or where are you today?
Ellis: Yeah, our pilot plant, so it has a nameplate capacity of 100 tons a year. Of course, the goal of the pilot plant is not to turn the crank. The goal of the pilot plant is to move as quickly as you can to optimize the design and the performance of the product produced. So optimizing all those parameters and then freeze that design and then scale it up as quickly as possible. So we are actively planning for our first commercial plant, and this would be used to produce tens of thousands of tons of cement per year. And so we are on track to have that plant commissioned by early 2026.
McNiel: Wow, that’s really exciting. What an amazing achievement for you to start a company in 2020 and now be producing cement that is certified. It’s certified as usable in construction.
Ellis: Yeah, that’s right.
McNiel: That’s impressive.
Ellis: Yeah, and I have to say, because I’m so lucky to work with people who really see this as an opportunity to have an impact and to have a legacy. And I think we say our mission is to have a swift and massive impact, and we measure that impact in the amount of cement we produce and sell. And I say this all the time, but I think when you’re working on climate, you get better people who work harder and who work better together. Because really, there are no individual wins. There are only collective wins when you’re doing something that matters so much.
“Really, there are no individual wins. There are only collective wins when you’re doing something that matters so much.”
McNiel: Well there are a lot of similarities between your business and our business. You’re producing a product that typically is associated with carbon. We’re producing energy, which is typically associated with carbon. We have a budget of 37 gigatons of carbon that goes into the atmosphere from producing energy. And if we can replace that with fusion energy, which produces no carbon at all — and TAE fusion, which produces no radioactive waste — then we’re giving people electrons without carbon. And you’re giving them concrete without carbon. And I think that’s a great thing.
The leaky tap analogy to understand the climate crisis
Ellis: Yeah, I think that’s really important, the technology-enabled carbon avoidance. I frequently use this leaky tap analogy for the climate crisis where you have a leaky tap and there’s three ways you can go about fixing the flood that this leaky tap is creating. And the first way is to fix the tap, which is the carbon avoidance. That’s what you and I are doing. We’re trying to keep the fossil fuel in the ground. But sometimes, as is the case for cement, that may not be the fastest way to fix the problem. And in that case, you get a bucket and you put the bucket underneath that leaky faucet and you collect the water that’s coming out. And that’s understood to be a patch solution. That’s post-combustion carbon capture to go with the analogy. And I think that may be necessary in the interim, but not a long-term solution like what you and I are trying to do. And then the third way to fix this flood is to start mopping the water off the ground. And so that in my mind is the direct air carbon capture.
McNiel: The hardest thing to do, too.
Ellis: Yeah, although I would say that in a world with limited resources and limited time, I do think focusing on step one and step two, and over-focusing on step three or paying exorbitant premiums for direct air carbon capture credits does feel like mopping up the ground before putting that bucket in place and before turning off the tap.
McNiel: Well, I think there are many people that would agree with you. We had a recent conversation about carbon capture, and it is a very challenging process to master.
One question I have for you before my final is, what’s the business model? I mean there’s certainly the model of producing cement. It’s a huge market. We know that 4 billion tons of cement at a $100 a ton, that’s a pretty good business, $400 billion business or more. Is your model just to produce bags of cement or are you going to license your technology and help other cement manufacturers sequester carbon or stop producing it?
Ellis: Yeah, we’re going to do whatever it takes to have that swift and massive impact. And so ultimately, that does mean taking what we do well, which is developing and perhaps operating this new electrochemical process and marrying that with what the incumbents do well, which is mining, crushing, grinding, producing on spec product and delivering it on time and keeping the trains going. It really is a logistics business, which is difficult, and they do it very well. And so, ultimately, I think the way we have a swift and massive impact is by working together. So presently, Sublime’s business is selling the cement product, and that’s until we get our first commercial plant up and running. And once that first commercial plant is up and running, we can use that as a reference so that we can de-risk the project finance needed to go and create more of these plants at a meaningful scale. At a scale that we can compete on cost so that we can work with other players and really deploy this all around the world, because there are many greenfield cement plants that are going to be built in the coming decades to service the increasing population. And we need to work as quickly as possible to make sure that those greenfield cement plants are built with next-generation carbon avoidance technology.
A vision for the cement industry in 2035
McNiel: With that in mind, you’re a young company, so you’ve got a long way to go. You have a goal of getting scale and getting to a million tons of produced cement and hopefully enabling some other concrete manufacturers in doing the same thing that you do licensing your technology. What do you think the world looks like in 2035 in the cement business? Are we going to get rid of carbon-filled cement?
Ellis: Yeah, by 2035, I think cement will be totally different. I think people are already moving to adopt new materials, to get comfortable with new recipes. And I think these performance-based standards and the push to really displace Portland cement, that is happening really at lightning speed. You know, I’ve been in this industry for five years because of course I’m an electrochemist and a battery person, but you know, we’ve brought on advisors with collectively 300 years of experience in this industry. And they said they’ve never seen the industry move so quickly on something. I really think that by 2035, the material we’re using to build our world will be a different material. And, if we’re successful, much of that material will be produced through Sublime’s process.
McNiel: Well, I certainly hope that you are. And, I’m super impressed and pleased with the progress you’ve made and the choices you’ve made in your career to pursue such important technology and innovation. So thank you very much.
Ellis: Thanks so much, Jim. It’s been a pleasure to speak with you.
McNiel: Thanks for listening to Good Clean Energy. Make sure to follow the show on Apple Podcasts, Spotify, or Google, or wherever you listen. And if you like what you hear, please give us a rating and a review. It makes a huge difference. I’m your host, Jim McNiel. See you next time.